Northampton Motorsport has been at the forefront of performance tuning since it was founded in 2002.
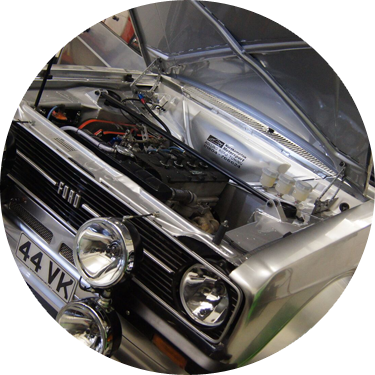
Rolling Road Introduction
One principle which applies to all engines is the need to provide the correct balance of air, fuel and ignition advance to ensure it will produce the optimum power output and efficiency.
When a manufacturer designs a production engine, many factors such as reliability, economy, driveability, emissions and cost have to be taken into account. All these factors mean that the end result is a compromise aimed at providing good all round performance. As part of the design process, the manufacturer will spend a great amount of time developing a system to provide the right amount of fuel and ignition for all driving conditions, again taking into account the need for good cold start performance, economy and reliable power.
As soon as any modifications to the engine are made, the original calibration of fuel and ignition will no longer be exactly correct and therefore the optimum performance available from the modifications may not be achieved. Simple changes like performance air filters or free flow exhausts may not affect the manufacturer’s calibration sufficiently to adversely affect drivability or performance. However, anything more fundamental such as a high lift cam, ported cylinder head or any significant change to the engine specification must be accompanied by a recalibration of fuel and ignition to achieve the best results.
The other thing which is common to almost all tuned cars is that this critical part of the tuning process is the one thing that is often neglected, resulting in disappointing power levels for the amount of money spent, and in the worst cases eventual engine damage.
How Dynometers work
The only way to accurately recalibrate fuel and ignition for a modified engine is to simulate the load imposed on the engine when driving, both throughout the rev range and at all throttle positions. This is done using a Dynamometer, which imposes a braking load on the engine and measures the torque reaction at the same time. There are two types of dyno’s, the engine dyno and the chassis dyno, which is more commonly known as a rolling road.
As the name would suggest an engine dyno requires the engine to be removed from the car and bolted to a purpose made rig, which is housed in a sound proofed cell and fed with cooling air and water. The fuel and ignition system as used on the car is also fitted to recreate the installed package as closely as possible.
The advantages of this set up are that torque is measured very accurately as the flywheel is physically bolted to the unit providing the braking force, hence the term flywheel power. Engine dyno’s are particularly good for engines producing very high power outputs or where specific and highly repeatable tests are required. Often engine dyno’s are used in the development of engines and tuning components because the rest of the car isn’t required at this stage. Engine dyno’s are more compact making the construction of a test cell easier as cooling and ventilation and sound proofing requirements are easier to manage.
The downside to testing your engine on an engine dyno is the need to remove the engine from the car and the fact that the final installed package of exhaust and intake systems and the enclosed nature of the under bonnet area in the car may cause the calibration requirements to change.
Also because engine dyno’s have very little inertia it is difficult to hold the engine under very light load or to calibrate over run and transient throttle conditions. This often results in engines that have been tuned on an engine dyno having to be “fine-tuned” on a rolling road afterwards.
Engine dyno’s are considered to be more accurate because there are no transmission / tyre losses to confuse the results. The other common problem with some twin roller rolling roads (cradle type) like our old Sun ram 12 is that wheel spin can distort the results making repeatable tests on light weight high power vehicles difficult to achieve.
Our Superflow rolling road is the single roller type with a large 30 inch roller which is lightly knurled to maximise tyre grip. In between the rollers is a powerful eddy current absorber unit that allows us to either impose additional braking load as the engine accelerates on the rollers during a power run or we can hold the engine at any RPM we wish to allow fine adjustments to the engines calibration.
The traction afforded by the large single roller means that wheel spin is no longer a problem and power and torque measurements are accurate and repeatable. Currently the most powerful front wheel drive car we have tuned is 600.4 bhp and the most powerful rear wheel drive was 860 bhp and 840 ft lbs torque.
A typical tuning session
Once we have checked the basics, oil, water tyre condition etc. we will get the car installed on the rollers and strapped down. We have over 50 tie down points anchored in the floor so in 14 years have never been unable to strap a car down and run it. Because the driven wheels sit on top of the roller and not in a cradle formed by two rollers there are no ground clearance issues. We have run everything from formula cars to trikes, police cars, ambulances and even an ice cream van!!
The bay has dedicated exhaust extraction plus powerful bay ventilation fans to keep the fumes down to a minimum. We also have a very powerful 3 phase cooling fan to direct air through the cars oil and water radiators.
Now we will install exhaust gas measuring equipment. Boost and knock detection equipment. The boost and fuelling are logged by the dyno and can be overlaid against power and torque to help with the tuning process. We also have an optical tachometer that can be used to measure wheel spin but we soon realised after getting the dyno that it was surplus to requirements as we just don’t get any.
We now gently warm the engine and transmission as well as the dyno, to make sure all the readings we get are at normal operating temperature. This also makes sure the engine is ready for full throttle and high rpm running. This is mainly for competition and performance engines and we will always respect any limits you wish to impose to engine rpm or throttle opening. We also use the dyno to run in new engines in a controlled environment.
We now use the dyno in a combination of steady state and transient modes to identify and rectify any calibration issues. We have a huge range of Weber, DellOrto and SU jets and needles as well as carburettor service parts, chokes and emulsion tubes. As well as a wealth of experience with Carburettors and classic and vintage cars we are also specialists in modern engine management systems. We are Agents for Omex and Life Racing engine management systems but we also map most other popular systems such as DTA, MBE, Emerald, Motec etc.
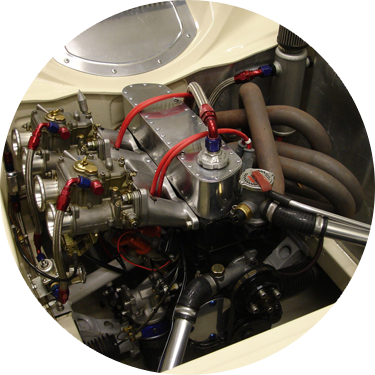